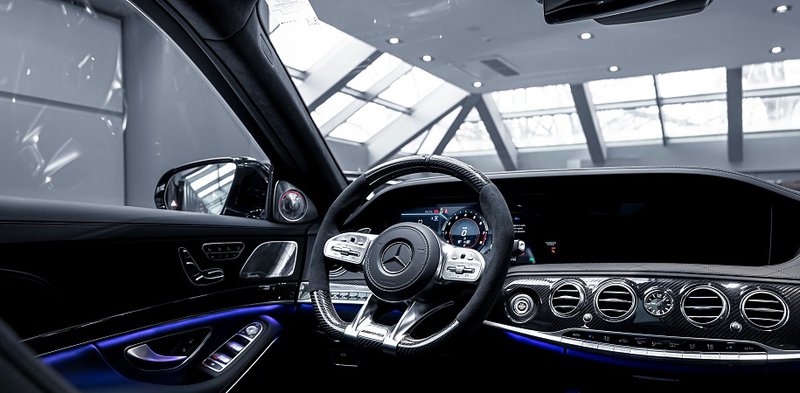
9 questions about automotive initial sample tests
How do automotive initial sample tests work these days? testxchange spoke to Alexander Grosch, Laboratory Manager Automotive Testing at ASO.
After giving an overview of initial sample testing in the automotive sector in a previous article, we would now like to look at the topic from a testing laboratory perspective. To this end, testxchange put forth nine questions to Alexander Grosch, Laboratory Manager Automotive Testing at Analytik Service Obernburg GmbH (ASO):
Mr. Grosch, how standardized or how individual are sampling requirements in general? Is testing predominantly carried out according to one simple (factory) standard, or does testing generally have to be carried out according to various additional individual requirements?
In order to prove the quality of products in the automotive sector, each OEM has issued numerous specifications that must be confirmed by an accredited laboratory, and in some cases, also a laboratory specifically approved by the OEM, as part of the initial sample tests. The specifications are usually defined in one or more delivery specifications. However, a delivery specification usually applies to very different components (e.g. VW's TL226 generally applies to painted components in the vehicle interior). In addition, there may be differences in the scope of testing depending on the installation location, material, or surface finish. A delivery specification generally only defines which test is to be carried out and in some cases also gives specifications. The actual tests are in turn described individually in separate test specifications or standards. These can again be test specifications of the OEM or general DIN or ISO standards, but also standards from the German Association of the Automotive Industry (VDA).
What is the general procedure for automotive initial sample testing in your testing laboratory?
In the best case, the customer starts his inquiry with a technical drawing of the sample and the specification according to which it is to be tested. In addition, the laboratory requires further information on orientation and the installation location in the vehicle (e.g. visible area), as well as a definition of the important surface areas in order to prepare a quotation. It is also important to know what material the component itself is made of and whether it is painted or metalized. The testing effort also depends on how many variants (e.g. different colors or base materials) are to be tested.
Depending on the customer data, individual quotations are prepared. In the process, we check which tests are needed and which aren’t, e.g. if the component is not in the vicinity. In addition, it is checked to what extent a standard-compliant test on the component itself is feasible, e.g. the specimen geometry or component size. Alternatively, special test specimens or test plates are to be manufactured from the appropriate granulate and, if necessary, painted.
Does a versatile testing service provider such as ASO usually carry out initial sample tests on its own, or are several testing laboratories used?
As Analytik Service Obernburg GmbH (ASO), we perform most of the tests ourselves. These include climate tests, weathering, sunlight simulation, light fastness, abrasion and scratch tests, various emission tests, and various chemical and physical tests. So the customer gets his measurements according to our motto: "Everything from one source". If despite the wide range of our own testing facilities, we are unable to carry out a test ourselves, we also have the complete portfolio of the SKZ Group at our disposal. In addition, we also organize such measurements at other approved testing laboratories and include their results in the overall final report.
What are the advantages of your institute compared to other competitors?
In addition to pure initial sample tests, we also offer damage analyses on a larger scale. If one or more tests reveal abnormalities in the component, we are able to support our customers in finding the cause.
What was the most unusual first article inspection you have experienced at ASO?
Here we would think of several orders, but according to our accreditation according to DIN EN ISO 17025 and especially according to IATF 16949 we are not free to talk about it with third parties. Confidentiality is an important requirement for us and our customers.
What are generally the biggest challenges in automotive initial sample testing?
The development processes for new components are taking place at ever shorter notice, with the times required for initial sample testing often being forgotten or insufficiently taken into account during planning. If pre-production is delayed by unforeseen problems, things get tight. Possibly, pre-reserved equipment times may also be forfeited as a result. Especially if long climate storage periods are prescribed, the duration of the analysis alone is predetermined by this and cannot be reduced.
Standards of different OEMs are often similar but differ in small details. This means that in some cases it is not possible to bundle analyses for different OEMs. It is also problematic that some OEMs prescribe special devices for testing so that different devices have to be kept on hand for different OEMs.
How have initial sample inspections changed over the last 20 years? What do you think have been the biggest change drivers here?
First article inspections are defined and specified by the OEMs and must be performed in qualified laboratories. Although these laboratories are accredited to DIN EN ISO 17025 and their competence has been proven via comparative tests, several OEMs require additional procedures to ensure that the laboratory's results are recognized. In some cases, this involves additional audits of the OEM on-site, some of which are very time-consuming. Only if one undergoes these procedures is one approved as a testing laboratory. After that, however, the laboratory can also take advantage of an additional listing, approval, or recommendation.
What developments do you expect for the future of automotive initial sample testing? (e.g., changed processes, more individual requirements, stronger standardization, etc.).
On the one hand, we expect that the approvals by OEMs described above will continue to increase, although accreditation according to ISO 17025 should actually be sufficient. On the other hand, digitization in the area of initial sample testing will also increase.
One trend in recent years is that the increase in functions that are being integrated into the components of the vehicle interior. These can be lighting or simple optical displays, but also large displays or sensors. As a result, the proportion of electrical tests is increasing. In some cases, pure current flow is sufficient, but in others, electrically controlled functions must also be tested under temperature, humidity, etc.
Another trend is the use of other/new materials. On the one hand, significantly higher-quality surfaces are being used. This in turn means more tests, adapted to the samples, for chemical resistance or scratch resistance. On the other hand, a development towards the processing of renewable raw materials and bio-based plastics can be observed.
The issue of emissions and odor in the interior is becoming increasingly important and the corresponding test requirements are becoming more complex. Whereas in the past it was primarily the individual parts that were tested, the requirements increasingly also concern entire system units that are tested as a whole. Corresponding tests require a large test chamber as well as detailed know-how. As ASO, we are also facing up to these changing demands and are in the process of setting up corresponding testing facilities at our company.
How do you assess the influence of advancing digitization in this context? Are your customers working on tools that will improve processes?
The rise of digitization can also be observed in initial sample inspections as far as the documentation of measurement results is concerned. This also includes measurement results being uploaded electronically from the test laboratory to the OEM portals. On the one hand, this procedure of direct transfer is more convenient for the automotive supplier. On the other hand, however, this also means a danger if deviations reach the OEM directly and unfiltered as errors. In our experience, when it comes to cases like this, it is easier if deviations are first discussed and evaluated in a personal meeting between supplier and OEM.