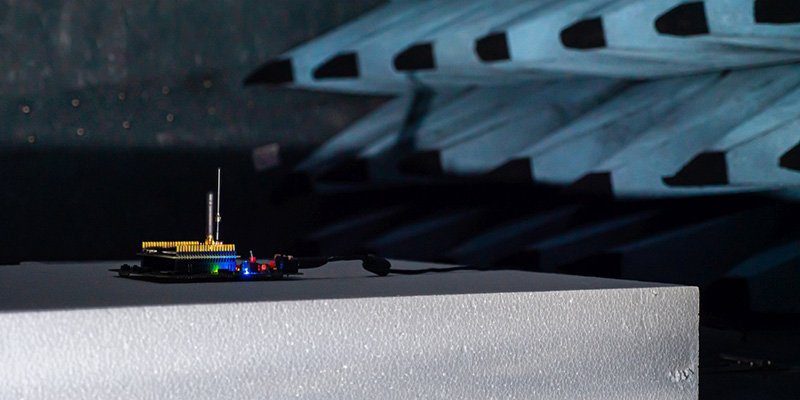
Failed EMC tests and how to deal with them
What happens if your product fails a crucial regulatory EMC test at an accredited testing lab? testxchange talked to EMC expert Markus Ridder, founder and managing director of waveLAB Ruhr, to discuss possible solutions to deal with that challenge.
testxchange: Markus, thank you for taking the time to talk to us today about EMC testing, specifically about what happens when a product fails an EMC test. To get started, can you please introduce yourself to our readers?
Markus Ridder: Good morning, thanks also from my side. My name is Markus Ridder and I am the managing director of waveLAB Ruhr, a company I founded recently in the Ruhr area in Germany. I am in my mid-forties and studied electrical engineering with a special focus on telecommunications in the 2000s. I then started working in the semiconductor industry, and got in touch with EMC topics very early on. At that time, I was responsible for EMC measurements for microcontrollers, and also took care of bringing our products into regulatory approval processes at accredited test houses. This is where I first got in touch with EMC topics, including EMC measurements, EMC standards and also EMC countermeasures. Later, I got into failure and damage analysis, mainly for electronics, before I worked at several accredited test houses, lately as a managing director at a bigger one. During that time I helped customers to overcome EMC and radio problems, often on their way to regulatory approval of their products. This honestly is my passion, which I am also following with my newly founded company waveLAB Ruhr.
testxchange: We can imagine that during all these years, you probably encountered numerous cases of products which failed EMC testing. What would the customers do in these cases and how would the accredited testing lab be able to assist in these situations?
Markus Ridder: There is no general answer to this question, but in my experience, about 90% of products do not pass all EMC tests right away the first time. Depending on the product, there are a number of tests such as radiated tests and conducted tests, and if only one of them fails, the ISO 17025 accredited lab has to issue a report with a “failed” result for this test. The lab’s quality management system does not allow it to manipulate the device under test (DUT) to achieve a better result. When the “failed” result occurs, a common problem is that the customer does not know how to overcome the issues. Furthermore, the testing manager at the test house often does not have the knowledge about how to implement EMC countermeasures like coils, like coupling capacitors or ferrites. So if a device fails, usually the customer takes the device, gets back into their own laboratory and does some trial and error. Eventually a second attempt for regulatory approval is made, hoping for the best, and the product then either passes all tests or fails again. In my opinion, it would be much better if this process could be made more efficient, both in terms of time and in terms of costs. So that it is not necessary to send the product back to the development department, but to make adjustments right after an issue has popped up during testing. If not directly in the lab, then maybe with experts closeby, and this is where waveLAB Ruhr comes in. We try to determine why a test has not been passed, and then to find the root cause of e.g. the limit violation. And then help the customer to overcome this issue.
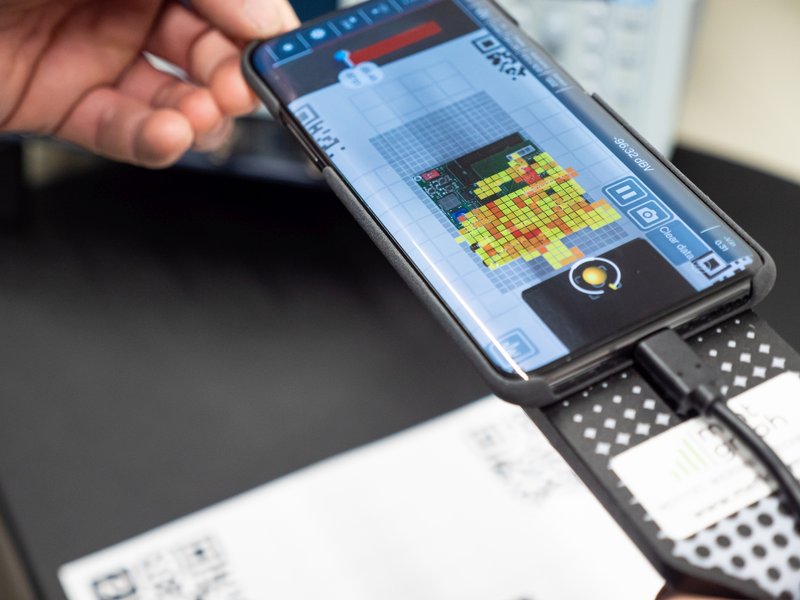
testxchange: Can you give us an example of one product and the steps you would take to help the customer with it?
Markus Ridder: Yes, let’s talk about a radio device that we worked with and which is not covered by an NDA. This device was a short range device with a transmission frequency of 868 MHz. The failure was found in so-called radiated spurious emissions testing (RSE); it was somehow the fifth harmonic that was violating the given limits for European type approval. The customer had quite a bit of knowledge and tried to reduce power, tried to reduce the used bandwidths to overcome the issue, but in the end, it was a question of the adaptive network that was placed close to the antenna. So the network had to be modified, which the customer would not have guessed by themselves. This is a good example where waveLAB could help. We were able to measure the RSE again. We saw the fifth harmonic being higher than the other ones and above the limit, of course. We then took care of adapting the network. So with different types of measurement equipment, like network analyzers, spectrum analyzers and near-field probes, we were able to get to the source of the problem. When we performed testing in our pre-compliance measurement chambers, we realized that the fifth harmonic could be reduced. So the customer entered the regulatory approval process again, this time with a much lower fifth harmonic than in the previous test. Overall, we think this was a very efficient, time and cost saving process.
testxchange: You mentioned that you have a pre-compliance test chamber. Would you advise all customers to perform pre-compliance testing as a general rule, and can they choose either an accredited or non-accredited lab for this?
Markus Ridder: The engineer inside me would say, it depends. It depends on the customer's experience. There are highly experienced customers who have had products in the market for quite a long time, and those often do not need pre-compliance testing. Then there are customers who come into contact with radio interfaces for the first time. Maybe they have experience with conducted communication and are now making the switch to wireless radio interfaces. For these kinds of customers, we really recommend pre-compliance measurements during the development process. This can be done by accredited test houses, many of which offer pre-compliance testing. It could happen, however, that these are quite expensive or have long lead times or are less flexible. Often they not only have accredited test equipment, but also huge test chambers that need to be paid for. Staff at these accredited labs usually know how to perform a testing procedure exactly according to a specific standard, but they may not necessarily understand specific details about the DUT and in which ways it may interact with specific test systems. How does a test influence the device? This is what waveLAB Ruhr does differently. We take physics into account. The standard is second, the electromagnetic fields, in either direction, both for emission and for immunity, are first. And this also applies to radio testing. So in general, we recommend making up one's mind during the development process regarding radio and EMC. If pre-compliance testing is needed here, we are pleased to help.
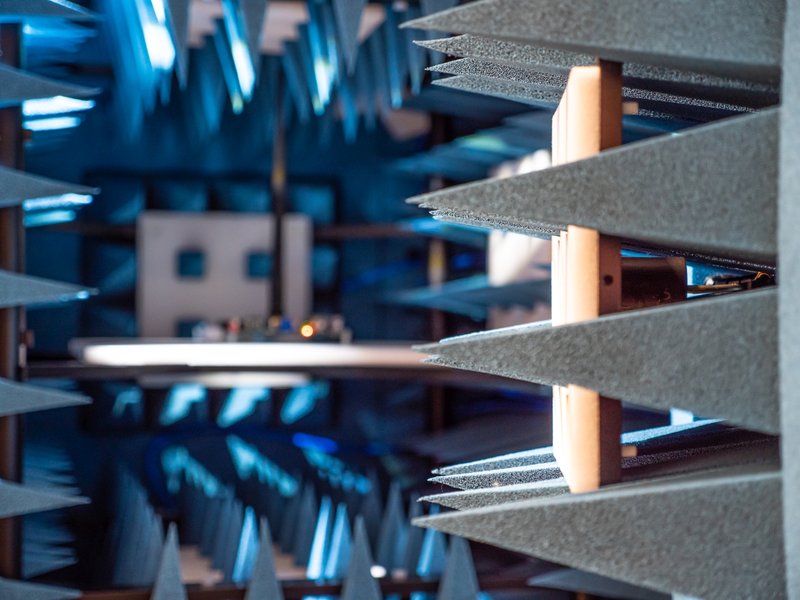
testxchange: Some customers may have observed that different accredited testing labs deliver different test results on the same DUT. And some may wonder if results from a non-accredited lab may differ even more. What is your opinion on the comparability of test results, especially between accredited and non-accredited labs?
Markus Ridder: In the end, one needs an accredited lab where your device passes the tests to bring the product into the market. Even though, one cannot compare test results between testing labs, accredited or not, without looking at the measurement uncertainties of each one. In my opinion, it is important to know your measurement uncertainties and put them into perspective instead of ignoring them. This makes any lab a good lab, accredited or not. In general, EU directives do not explicitly require testing before a declaration of conformity can be written.You as a manufacturer sign the document and this makes you legally responsible for this device meeting the requirements from the respective directives, which is totally independent from the kind of lab one chose. So when you sign such a declaration, it would be common that an accredited lab has performed regulatory testing. How do the test results of such an accredited lab compare to the test results measured by a non-accredited lab like mine? One main difference is that I do not have an ISO 17025 quality management system. I do have calibrated equipment, but not calibrated according to ISO 17025. So when we talk about the comparability of test results, where does a non-accredited lab have its place? One important thing to keep in mind is that we (as all others) do validation measurements for all types of equipment. Additionally, if you receive a DUT from an accredited test house, you usually get their test reports and you can see: Okay, this is a frequency where the violation takes place. Do I see the same frequency in my equipment? The answer must be yes, always. If not, there is something wrong with my equipment. Regarding the amplitude, I should see the same behavior/value as seen in an accredited lab. So, if the fifth harmonic is above the limit in the accredited test report, the fifth harmonic should be above the limit in my case. If I then reduce the amplitude by 3 dB, or 6 dB, for example, I should see about the same effect as an accredited lab would see. So if we have a violation of 12 dB in the accredited lab, a reduction of 6 dB my measurement chamber will not be sufficient. So usually I would also strive for having some space like 20 dB between the limit violation and the final amplitude.
testxchange: In this context, are round-robin tests something that also non-accredited labs do to compare their results with other labs? If yes, is this common?
Markus Ridder: Honestly, I do not think it is common between non-accredited labs. Maybe in my case, it is different. I founded a group of round-robin testing laboratories in Germany in 2017. We are now 13 accredited test labs plus waveLAB as a non-accredited test lab. So I participate in round-robin testing with this group. Accredited labs need round-robin testing once a year for each and every discipline, in order to comply with DAkkS requirements. As I founded this group, I still have regular contact with it and I think it is also valuable for exchanging ideas between labs. For example regarding equipment for radiated emission testing. Are other labs using a comb generator or other equipment? The exchange between knowledgeable people is very fruitful and important. So for my non-accredited lab, it makes a lot of sense to take part in round-robin testing. These tests are even free of charge, as all labs in the group take turns to organize another round-robin test, so it is not up to one single company.
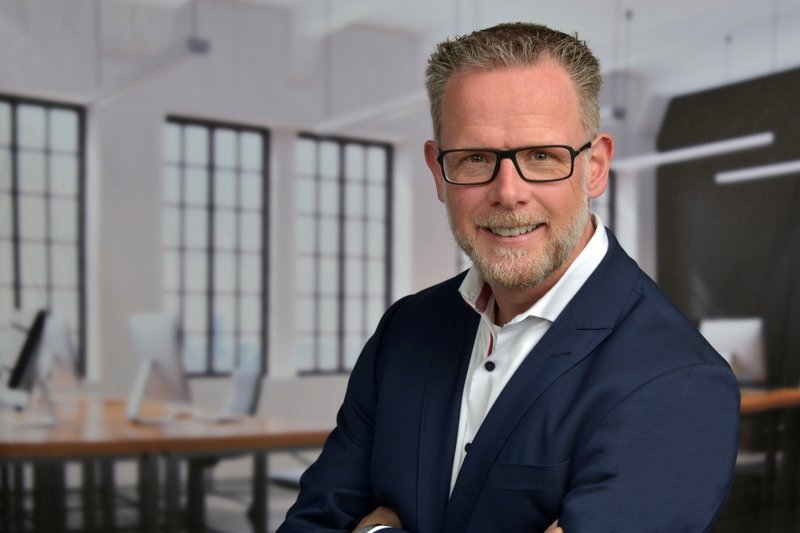
testxchange: When it comes to EMC testing in general, are there trends and challenges that you see coming up on the horizon?
Markus Ridder: One important topic right now is frequency extension, in terms of ETSI requirements. There are groups inside ETSI who are currently discussing the extension of frequencies for radiated emissions for EMC testing. As of today, these tests usually have been tested up to 6 GHz. The same applies to immunity. ETSI is currently working on the topic of 40 GHz frequency range. This is because they are taking care of the 5G technology and 5G millimeter waves starting at 24 GHz. And they want to cover up to 40 GHz immunity and also emission. I think this is a new challenge, especially for the accredited test labs that are active today. Many of their semi-anechoic chambers do not cover more than 6 GHz. So they have VSWR or NSA measurements to cover up to 6 GHz, and their equipment is not suitable to test up to 40 GHz. 40 GHz immunity also is quite a big challenge. The amplifiers for this are quite costly and this is also something that waveLAB and other labs will have to deal with to compete in the future. As of today, we are not ready to deal with 40 GHz, but we are getting close to 20 GHz, so we are on a good way. In conclusion, 40 GHz is an important challenge that especially developers need to be aware of.
testxchange: Markus, thank you very much for your time!
Markus Ridder: Also from my side it was a pleasure.